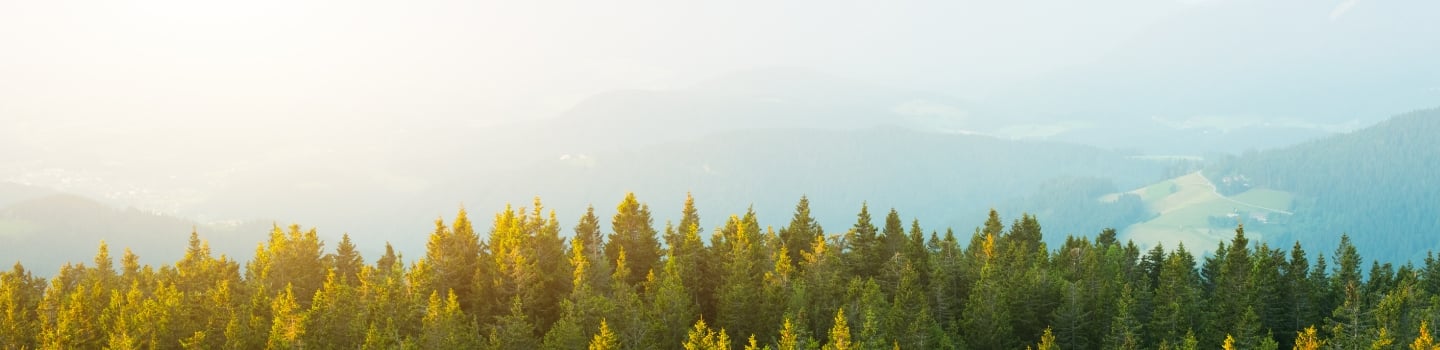
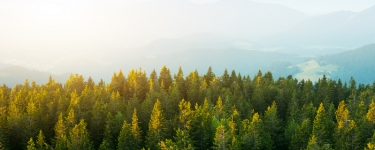
SUSTAINABILITY
NEWS
-
Mitsubishi Heavy Industries, Ltd.
Ministry of Energy of Uzbekistan and MHI Sign MOU to Conduct Joint Study of Decarbonization Strategy for Uzbekistan -
Mitsubishi Heavy Industries, Ltd.
MHI Marine Machinery Begin Demonstration Testing of Methane Oxidation Catalyst System for Marine LNG Engines -
Mitsubishi Heavy Industries, Ltd.
MHI Launches "Prismo," a New Brand Eco-Friendly Next-Generation AGT -- Reducing CO₂ Emissions Through Manufacturing at Mihara, Hiroshima, a Factory Aiming To Reach Carbon Neutrality -- -
Mitsubishi Heavy Industries, Ltd.
MHI Thermal Systems Receives JSRAE Technology Award -- Recognized for Development of a Large-Capacity Centrifugal Chiller that Uses a Low-GWP Refrigerant -- -
Mitsubishi Heavy Industries, Ltd.
Mitsubishi Shipbuilding Acquired Approval in Principle (AiP) from Classification Society for the Basic Design of an Onboard Carbon Capture and Storage System
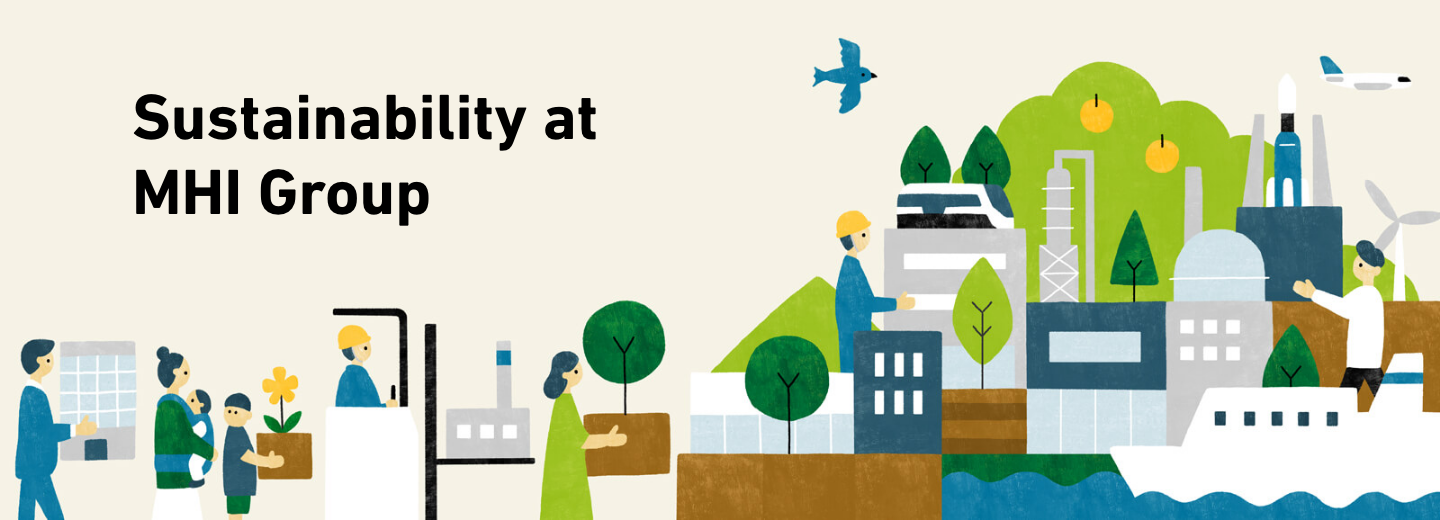
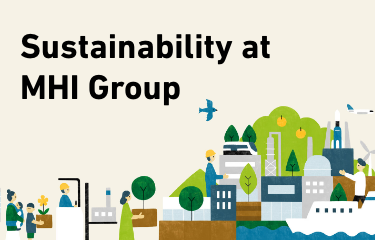
Solving society's most pressing issues with manufacturing technology
The Mitsubishi Heavy Industries (MHI) Group will contribute to the realization of a more sustainable society
by providing outstanding products and technologies.
We are focused on leveraging our proven track record of advancing decarbonization solutions
to help achieve a carbon neutral world.
SUSTAINABILITY DATABOOK 2024
![]() To download the latest SUSTAINABILITY DATABOOK, which provides information on our sustainability management strategies, initiatives and progress in addition to detailed data on social, environmental, and governance, click here |
-
MHI REPORT 2024