MHI's Response to the Great East Japan Earthquake
MHI's Response to the Great East Japan Earthquake
MHI Group relief support activities as of March 23 are as follows.
Customer support measures
Support to electric power companies
- Restoration work at MHI-supplied power generation facilities in affected areas, with 15,740 MW now restored (98% of pre-disaster levels).
- Emergency provision of 5 gas turbines to serve as new power supplies; construction relating to 2 units of TEPCO(Chiba) already completed.
- Completion of support to install 2 gas turbines loaned gratis by EGAT of Thailand.
- Free loan of 5 electric vehicles for business use at electric power companies.
- Provided a total of 143 portable generators equipped with Meiki engine.
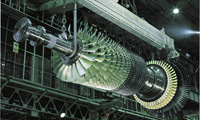
Support to Fukushima No.1 Nuclear Power Plant
Providing proposals and cooperation useful to recovery efforts based on common nuclear power technology even though the reactors used at Fukushima plant are different from the pressurized water reactors (PWR) handled by MHI.
- Performed conversion work at Yokohama Dockyard & Machinery Works on "Mega-Float" provided to TEPCO by Shizuoka City to store large volume of water pooling at the reactors.
- Delivered 2 specialized vehicles built on 15-ton forklift bases to clear rubble near the nuclear power plant.
- Delivered and installed storage facilities for radioactive sludge produced during treatment of contaminated water.
- Selected along with Toshiba Corporation and Hitachi-GE Nuclear Energy, Ltd. to participate in the Japanese government's project to develop technologies to deal with accidents at nuclear power plants. Developing technology for future removal of nuclear fuel.
- In response to requests from TEPCO, feasibility studies are in progress for treating contaminated water, shielding against radiation, preventing spread of radioactive materials, etc.
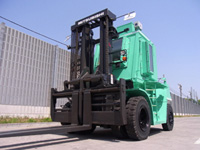
Other support activities
- Lent support for restoration of local waste treatment facilities damaged by the tsunami. Currently responding to inquiries from affected municipalities and other groups regarding simple incinerators (widely used after the Great Hanshin Earthquake)
- Response under way toward restoring social infrastructure – bridges, electronic toll collection systems, beverage fillers, newspaper rotary presses, paper converting machinery, etc. – in the disaster-affected areas.
- Supporting affected customers to restore machine tools and air-conditioning systems; a product support system has also been established.
Relief support to disaster areas
Relief assistance and fund-raising campaigns
- MHI Group to provide relief assistance equivalent to approx. 500 million yen.
Total includes monetary aid and emergency supplies. (for daily needs, etc.) - Relief fund-raising campaigns were conducted at the Head Office and all company works. Approx. 45 million yen has been collected, and the company plans to provide a matching amount, for a total value equivalent to 100 million yen.
- Donation to the Global Fund for Educational Assistance to provide scholarships to students affected by the disaster.
- Donation at the International Smart Grid Expo and the Renewable Energy World Fair.
- Donation to the Tohoku University ECEI Eastern Japan Earthquake Recovery Fund.
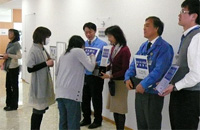
Support of medical activities
- Transportation of medical supplies to Fukushima region using company aircraft. Approx. 500kg (arranged through Nagoya Medical Association) was transported by 2 flights on March 19 (from Nagoya Airfield to Fukushima Airport).
- Dispatch of doctors and nurses from company medical facilities (Mitsubishi hospitals) at request of Japan Medical Association et al.
- Mitsubishi Nagasaki Hospital
- : 1 nurse assigned to Kesennuma City (Miyagi Pref.) from March 31 to April 5.
- Mitsubishi Kobe Hospital
- : Dispatched 1 medical doctor to Fukushima Prefecture from March 24 to May 11; additional doctors will be sent at request. Dispatched 1 nurse to Ishinomaki City (Miyagi Pref.) from May 6 to 10, and again from May 22 to 26.
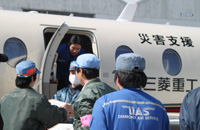
- Cooperation in receiving patients at company medical facilities (Mitsubishi hospitals)
Notification of acceptance at 5 company hospitals (Nagasaki, Kobe, Nagoya, Hiroshima, Mihara) sent to Japan Medical Association.
Provision of company facilities for disaster victims
- Registration with local governments of company facilities available to disaster victims. The results at the time the program was wrapped up at the end of December 2011: in company housing: 179 households at 10 locations; in company dormitories: 111 persons in 5 locations; in company recreational facilities: 285 persons in 2 locations.
- Offered 9 company housing units at Sagamihara Machinery Works to companies in affected areas.
"Support Tohoku" project at company dining rooms (with DS Food Service Co., Ltd.)
- Menus feature foods and alcoholic beverages (night shift) from the disaster areas, now victim to fear mongering. Provided approx. 1,000 meals in total at the Shinagawa Head Office Building and the Yokohama Building, employee dorm dining halls, etc.; progressively expanding to company works, etc. nationwide. Introduced into dinner menu at Yokohama Dockyard & Machinery Works.
- 10 percent of alcoholic beverage sales to be allocated to relief fund.
- Display and sale of local specialty products of the disaster areas.
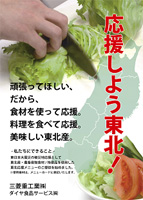
Tohoku Product Fairs
- To support specialty products from the disaster areas, from June 14 to 16 a "Tohoku Product Fair" was held at the Shinagawa Head Office Building for company employees and employees at neighboring companies. Similar events were conducted by company works (Nagasaki Shipyard & Machinery Works, Kobe Shipyard & Machinery Works, Yokohama Dockyard & Machinery Works, Takasago Machinery Works, Nagoya Aerospace Systems Works, Nagoya Guidance & Propulsion Systems Works, Hiroshima Machinery Works, Mihara Machinery Works, Sagamihara Machinery Works, Nagoya Air- Conditioning & Refrigeration Machinery Works, and Ritto Machinery Works) in conjunction with summer festivals, etc., for their employees and local communities.
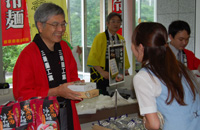
Dispatch of employee volunteers
- Approx. 110 employees from the Tokyo area (Head Office, Yokohama Dockyard & Machinery Works, Sagamihara Machinery Works) were dispatched to the disaster areas as volunteers. There were 3 dispatches between May 24 and June 10, each lasting 4 days and involving 24-40 employees. Locations were evacuation centers in Kesennuma, Minami-Sanriku and Tome in Miyagi Prefecture. Activities included cooking, cleaning of evacuation centers, and delivery and sorting of relief supplies.
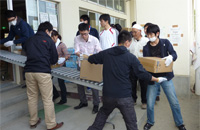
- The DynaBoars, the rugby team of the Sagamihara Machinery Works, conducted rugby clinics in Sendai City on April 24 and in Ishinomaki City on May 22 and June 26; a total of 220 people participated, from primary school children to adults. On April 25 and July 11 the DynaBoars helped disaster victims clear mud from their homes and performed similar chores.
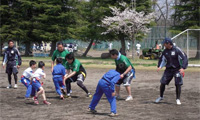
- On July 5-7, 6 new employees at the Ritto Machinery Works, machine tool business headquarters, helped clear mud from homes and farmlands in Higashi-Matsushima City (Miyagi Pref.)
- On July 19-20, 7 employees from the Nagoya Aerospace Systems Works performed cleaning, etc. of stricken homes and hotels in the cities of Ofunato and Rikuzentakata (Iwate Pref.)
- On July 30, 51 employees from the Head Office, including the Tohoku Branch, performed rubble removal and sorting work, etc. in Rikuzentakata.
- On September 6 and 7, 55 new employees and others from the Kobe Shipyard & Machinery Works performed rubble removal and cleanup at the fishing port in Ishinomaki.
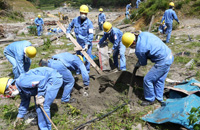
- On November 17 and 18, 24 new employees and others from the Yokohama Engineering Center removed weeds and cleared irrigation channels in fields damaged by the tsunami in Rikuzentakata.
- On June 15, a mosaic of messages of support and encouragement created by 132 new employees at the Nagasaki Shipyard & Machinery Works was presented to the people of Tomioka (Fukushima Pref.). As part of this project, on May 30 employees in Nagasaki and Hiroshima went out into the streets and collected 600,000 yen in donations, which were sent to the stricken region through the Japan Red Cross.
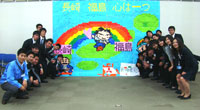
- In mid August, employees of the Power Systems business headquarters at the Yokohama Building organized the Minato Mirai Memory Restoration Brigade, a group of volunteers who clean photographs damaged in the disaster. So far over 700 people, including volunteers from nearby offices and local residents, have signed up and more than 45,000 photos have been cleaned.
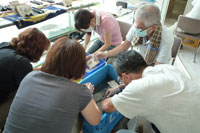
- On September 28, a workshop was held at the Nagoya Aerospace Systems Works to teach aircraft riveting skills to 10 students from Kesen Junior High School in Rikuzentakata. Another such workshop was held on December 16 for four students from Yonezaki Junior High School, also in Rikuzentakata.
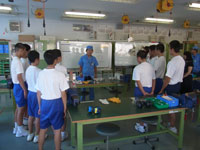
- On July 28, at elementary schools in Minami-Sanriku, employees conducted science classes for 200 students using the wakamaru robot and taught the principles of flying through crafting of paper airplanes.
- On October 21, at elementary schools in Morioka (Miyagi Pref.), employees conducted science classes for 105 students using the wakamaru robot.
- On November 13 and 14, employees conducted science classes in Kushiro (Hokkaido) for 110 elementary school students and 200 high school students.
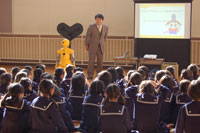
- On November 3, 4 and 5, employees performed a charity musical in Rikuzentakata, with a total of 620 elementary school students and local residents attending.
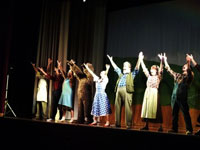
Other activities
- The company donated and installed 13 air-conditioning units at evacuation centers in the towns of Otsuchi and Yamada in Iwate Prefecture.
- The company donated 20 forklift trucks to support recovery work at fishing ports in the cities of Miyako (Iwate Pref.), Kesennuma (Miyagi Pref.) and Ishinomaki (Miyagi Pref.).
- The company also donated air purifiers, solar energy generating systems, and other relief materials.
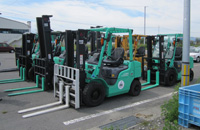
Energy Conservation Measures for 2011 Summer Peak Season
In addition to the various measures taken to reduce summer peak power usage by 25percent vs. 2010, the initiatives indicated below enabled the company to achieve power use reductions of 31percent in July, 29.1percent in August and 33.1percent in September. (Shinagawa and Yokohama Head Office buildings, Yokohama Dockyard & Machinery Works, Sagamihara Machinery Works)
- Expanded operation of stand-alone power generators at Shinagawa Head Office, Yokohama Dockyard & Machinery Works and Sagamihara Machinery Works
- Introduced extended holiday plans at the Shinagawa Head Office Building and the Yokohama Building for 10 days in July (16-25) and 12 days in August (11-22). Some holidays originally scheduled in the autumn and after will be converted to work days.
- Partial changes will be made to the summer holiday schedules at the Yokohama Dockyard & Machinery Works and Sagamihara Machinery Works. From July through September, some Mondays will be taken as holidays and some Saturdays will be workdays.