Press Information
MHI Machine Tool to Include Its DIASCOPE Machine Tool Monitoring System as Standard for All Machine Tools
-- Expanding the Customer Support Function to Strengthen Market Competitiveness --
-- Expanding the Customer Support Function to Strengthen Market Competitiveness --
・ DIASCOPE to be included in units sold from April 2020, maintenance support contract also being renewed
・ Monitoring system and regular maintenance to ensure stable operation, and improve LCC
Tokyo, February 10, 2020 - Mitsubishi Heavy Industries Machine Tool Co., Ltd., a part of Mitsubishi Heavy Industries (MHI) Group, will include its monitoring system DIASCOPE as standard equipment in all machine tools sold from April 2020. This system utilizes efficient IoT (Internet of Things) technologies that integrate distributed processing at the edge(Note1) with cloud (Note2) services, in order to make machine tools more intelligent, autonomous, and optimized. By providing full support and improvements for customers' production activities throughout the value chain, MHI Machine Tool aims to strengthen its market competitiveness. The maintenance support contract with customers will also be renewed. MHI Machine Tool will enhance its customer support functionality to develop services focused on digital transformation(Note3).
The DIASCOPE service to be provided as standard is a fully renewed version of the monitoring system already offered under the same name. It will be incorporated in all types of machine tools, including large machines, gear machines, and micro milling machines. The main points of the renewal are that collection and analysis of a broad range of data is conducted in remotely located cloud servers via the internet, while data collected from the machine tool sensors and measuring instruments is handled with a distributed processing setup using nearby edge servers. This arrangement allows for fast and efficient monitoring.
The incorporation of DIASCOPE will provide users with various services for remote and operational monitoring. With remote monitoring, when a problem occurs the MHI Machine Tool's support center is automatically notified of the alarm information through DIASCOPE, allowing for prompt restoration of service. This will help to lessen the downtime for the machine. Operational monitoring includes functionality to confirm in real time the operating status of a machine at any time and from any location through a computer or smartphone, giving users quicker notification of machine stoppage, such as when an alarm is signaled or the process has concluded. Users also have access to an analysis of the operation record just by looking at a control panel screen or a mobile phone, allowing for immediate measures to improve operability.
Going forward, MHI Machine Tool plans to successively offer a range of services that connect the user with its support center, such as functionality allowing two-way communication through the control panel screen or a smartphone, as well as portal or processing network sites that provide various types of information.
The renewed maintenance support contract will ensure greater operational stability of the equipment by providing for regular maintenance, and improve the life cycle cost (LCC) for the customer. In addition to the current type of annual contract, MHI Machine Tool will offer a greater range of contract plans, such as long-term and simple maintenance plans, providing a broad range of support for stable operation and machine accuracy.
MHI Machine Tool's maintenance support contract has been well received by many customers since its launch in 2016, with a total of approximately 200 units (around 100 companies) covered. Customers under contract have around a 50% reduction in unexpected stoppage, contributing to improved production.
Going forward, MHI Machine Tool will further expand its support contract service menu, and with a lineup that includes maintenance support plans that enhance the machine maintenance skills of customers, will provide support not only for hardware, but training and other services as well.
MHI Machine Tool, by offering a series of digital transformations, will focus on providing finely detailed solutions more closely tailored to on-site production.
- 1Edge (edge computing) is a computer processing method in which servers and computers are distributed in locations near terminals (the "edge"). Also called "edge processing," the distribution of the computing load provides such advantages as shorter communication times.
- 2Cloud (cloud computing) is a method of providing computer resources in remote locations (the "cloud") as a service via the internet or other computing network.
- 3Digital transformation is the concept of changing the lives of people for the better in every respect through the widespread use of IT. In the business world, the term is mainly used to imply companies utilizing technology to reform or stimulate their business performance or domains in a fundamental way.
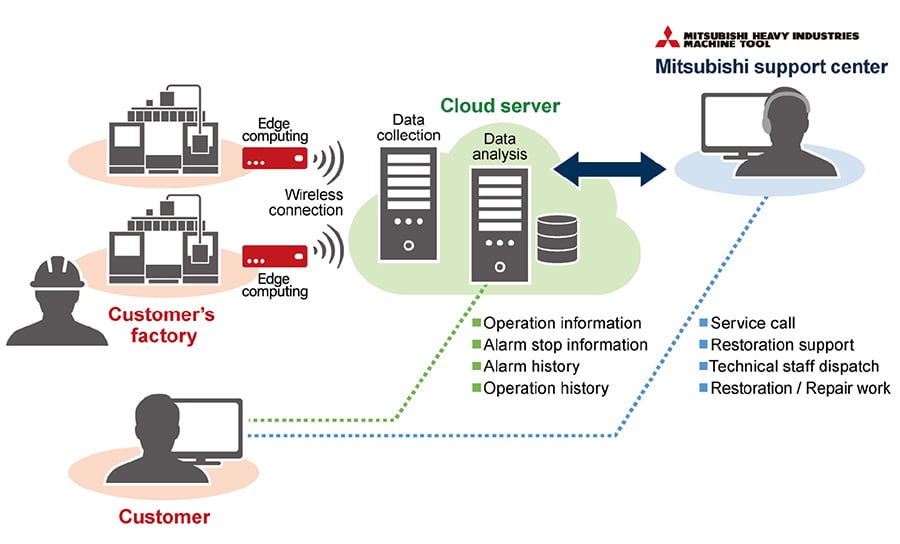
About MHI Group
Mitsubishi Heavy Industries (MHI) Group is one of the world’s leading industrial groups, spanning energy, smart infrastructure, industrial machinery, aerospace and defense. MHI Group combines cutting-edge technology with deep experience to deliver innovative, integrated solutions that help to realize a carbon neutral world, improve the quality of life and ensure a safer world. For more information, please visit www.mhi.com or follow our insights and stories on spectra.mhi.com.