Press Information
MHI Group Presents “Best Innovation 2022” Awards for Activities that Contribute to Mitigating Impacts on the Global Environment
-- Target on Achieving a Sustainable Society through Ongoing Advances in the Company’s Growth Strategy Areas --
-- Target on Achieving a Sustainable Society through Ongoing Advances in the Company’s Growth Strategy Areas --
・ Awards recognize business activities that contribute to global environmental preservation and protection, and raise environmental awareness among Group employees
・ Recognition of products and technologies that contribute to Company’s two growth strategy areas – Energy Transition and New Mobility & Logistics – and boost safety and security
・ Awards program adds momentum to realization of a sustainable society, resolution of social issues, and achievement of a carbon neutral world
Tokyo, February 16, 2023 – Mitsubishi Heavy Industries, Ltd. (MHI) has presented its “Best Innovation 2022” awards to 20 products, technologies and services related to its business activities and growth strategies that contribute to the preservation and protection of the global environment and mitigation of environmental impacts, thereby contributing to realization of a carbon neutral society. Through this in-house program, the Company aims to raise environmental awareness and encourage further innovation among its Groupwide employees.
Of this year’s 20 award-winning recipients, here we introduce 10 innovations related to the Company’s strategic growth areas that will contribute to reduction of environmental impacts.
Specialized safety facility for nuclear power plants
Mitsubishi Heavy Industries, Ltd., Nuclear Energy Systems
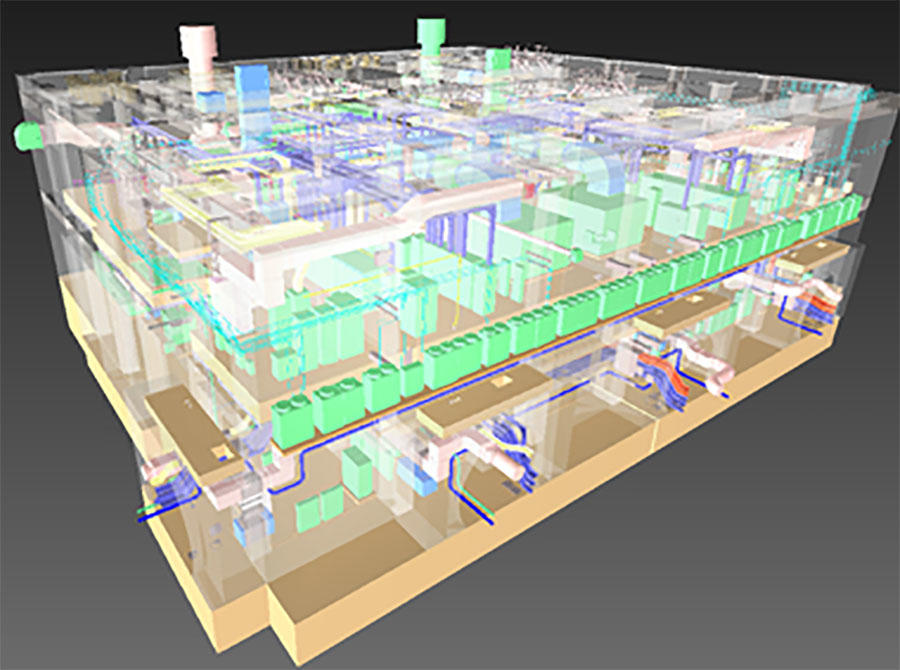
Specialized Safety Facility Image
MHI safely completed the design, manufacture, inspection, on-site construction and trial operation of a specialized safety facility (SSF) for nuclear power plants (NPPs), in response to calls for their installation under what are said to be the world’s most stringent new regulatory standards. From formulation of the basic concept through to facility construction, MHI quickly completed the SSF for a pressurized water reactor (PWR) NPP, and based on its performance results and the acquired expertise, the Company have proactively been also working on an SSF for a boiling water reactor (BWR) NPP. As Japan’s first facility specifically targeting backup safety and anti-terrorist protection, SSFs will further improve the safety and reliability of NPPs. The development project also demonstrated the outstanding level of MHI Group’s comprehensive engineering capabilities.
Compact CO2 capture system enabling easy transport and installation
Mitsubishi Heavy Industries Engineering, Ltd., Decarbonization Business Department
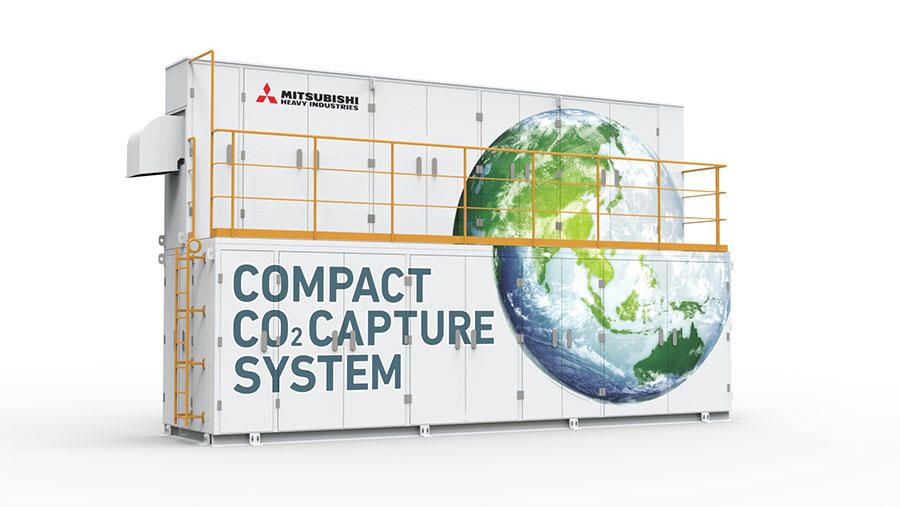
Compact CO2 Capture System
MHIENG developed a compact CO2 capture system to contribute to carbon neutrality for small to medium scale industrial emitters by applying the Company’s proprietary “KM CDR Process™” (jointly developed with The Kansai Electric Power Co., Inc.), which has been applied to large-scale facilities such as power generation systems, chemical plants, etc. Standardized modular design enables lower cost and shorter lead time as compared to conventional approach, and it also provides easy transportation and installation in locations with limited space. These enhancements have expanded the range of applications of “KM CDR Process™” and exemplified by the system’s adoption in the first commercial operation at a biomass-fired power plant. Demonstration testing has already been conducted at a waste incineration facility (waste-to-energy plant), a cement plant and gas engine application. Today the lineup is being expanded and a fully integrated customer support system is under development that will encompass new services such as automated operation and remote monitoring and after sales servicing. The new compact CO2 capture system has been named “CO2MPACT” (trademark registration pending), and with the name MHIENG will aim for a stronger market presence worldwide.
TPQC, a system that automatically optimizes the entire production process of steel products
Primetals Technologies
Primetals Technologies has introduced and commercialized the “Through-Process Quality Control System,” (TPQC) – an IT solution that comprehensively optimizes the entire production process of steel by recording high-resolution data and by providing the centralized collection of quality, process and equipment related data. Also, TPQC enables steel producers to to reduce losses from quality deterioration caused by production process deviations, and contributes to energy savings and the reduction of carbon emissions. In addition, TPQC can partially compensate the lack of qualified personnel in steel production by digitizing and applying production know-how.
EVOL, ultra-high-speed box making machines enabling twin box cutting
Mitsubishi Heavy Industries Machinery Systems, Ltd., Printing & Packaging Machinery Headquarters
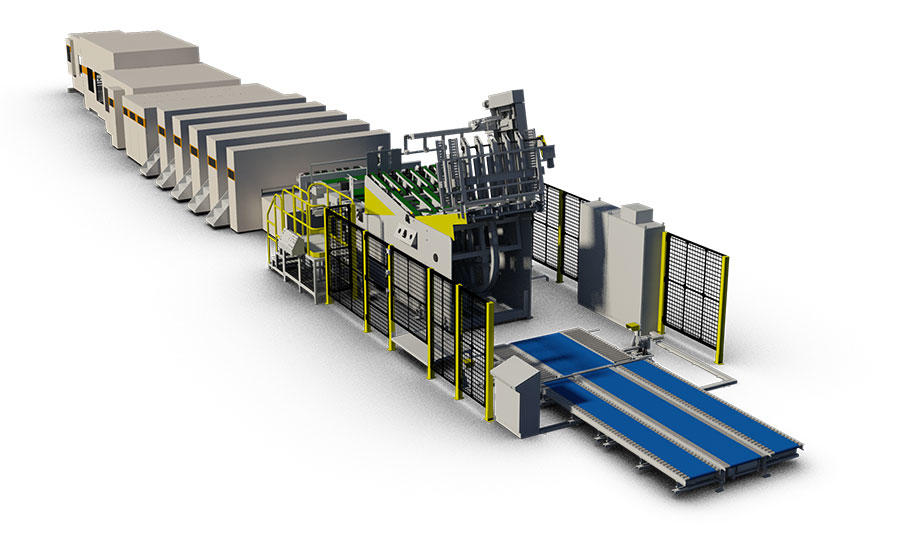
EVOL, ultra-high-speed box making machines
enabling twin box cutting
Performance of the EVOL, MHI-MS’s best-selling corrugated box making machines, has been newly optimized with the addition of two peripheral systems: a dual slotter unit (DSL) and prefeeder (MPF). Conventionally, one corrugated sheet is used to make one box; but with the DSL, two boxes can be made from a single sheet, thereby doubling production capacity. The MPF enables automated stable paper feeding to the EVOL at high speed. With the earlier EVOL, from 400 sheets a maximum of 400 boxes per minute can be printed, slotted, creased, pasted and folded, generating stacks of 20 to 25 boxes per operation. But with an EVOL equipped with the DSL, the same 400 sheets can yield up to 800 boxes per minute. With the synergy derived from a high-reliability after sales servicing system, the newly enhanced EVOL has already garnered strong support from users in North America and around the world.
Video introducing the EVOL: https://youtu.be/j7eWsLbzIoE
Reduction of carbon emissions through provision of large-capacity centrifugal chillers for high-efficiency district cooling
Mitsubishi Heavy Industries Thermal Systems, Ltd., Chiller & Heat Pump Engineering Department
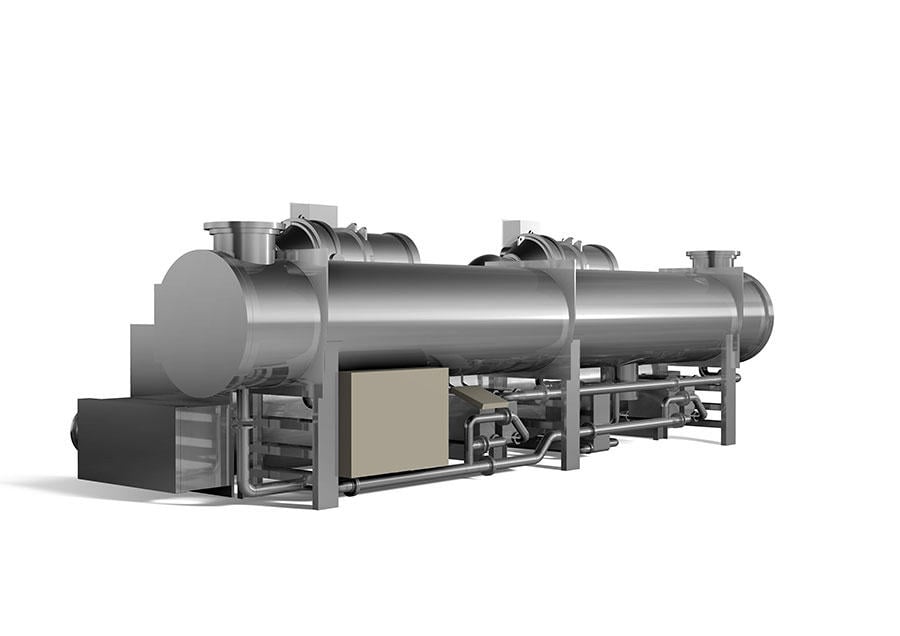
Parallel Type Centrifugal Chiller
MHI Thermal Systems has commercialized high-efficiency, large-capacity parallel (i.e., featuring dual compressors) centrifugal chillers that consume minimal energy and are adaptable to lower environmentally impact refrigerants. As the global strategic product for the centrifugal chiller business, to date approximately 70 parallel type centrifugal chillers have been delivered mainly for the district cooling plant and semiconductor factory in the Middle East, Singapore, Korea and Japan. Their outstanding quality and high reliability have contributed significantly to enhance market recognition of MHI Thermal Systems in the global market. In addition, they also have contributed to reduce the carbon emissions substantially along with environmental protection by the adoption of lower environmentally impact refrigerants and higher energy efficiency characteristic compared to the conventional machine.
Reusing processed waste material from the composite aircraft wing in household application
Mitsubishi Heavy Industries, Ltd., Commercial Aviation Systems
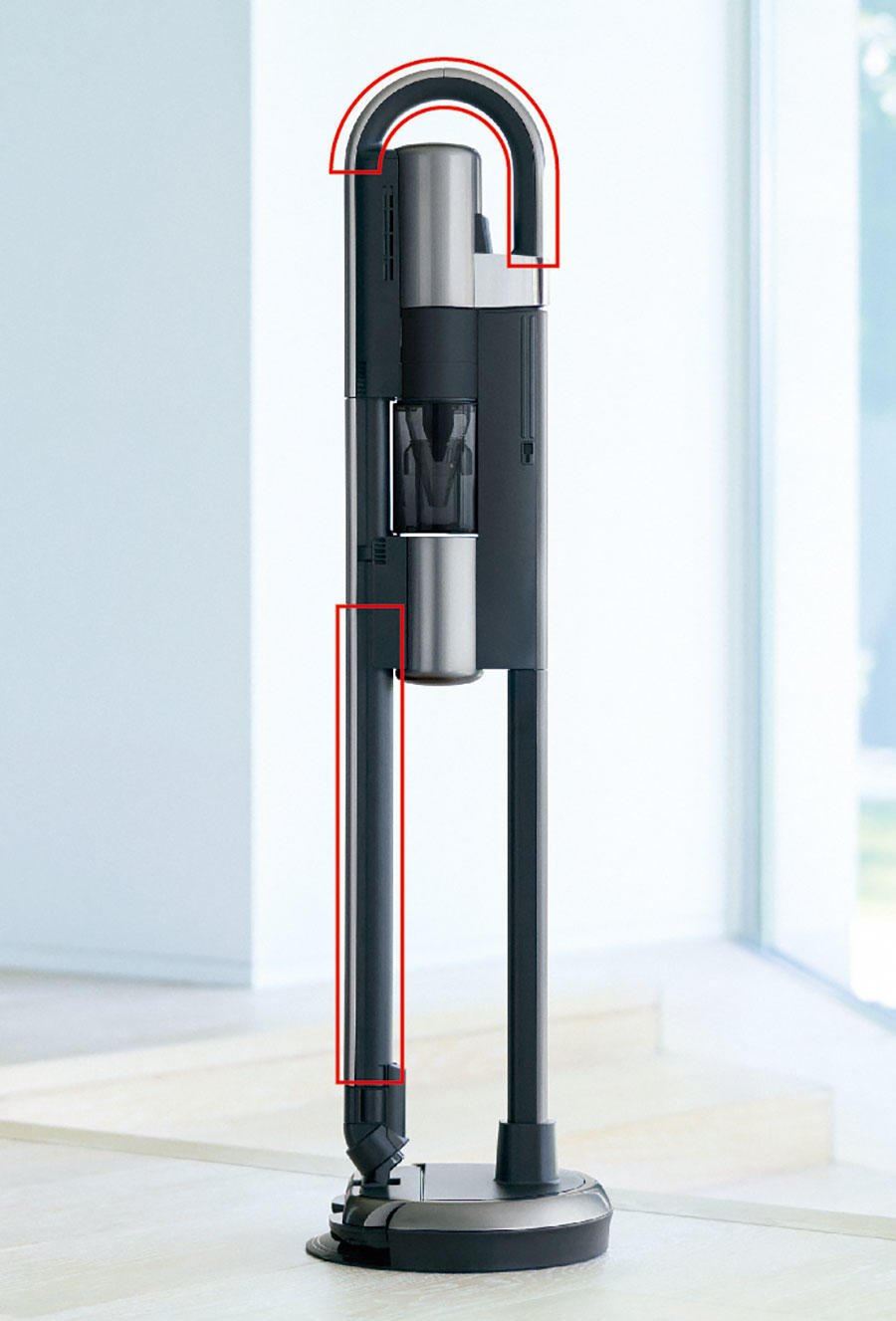
Mitsubishi Electric iNSTICK
ZUBAQ cordless cleaner
Waste materials from composite wings produced for Boeing’s 787 mid-size aircraft is being reused in household application. Carbon fiber waste material generated during the wing production process is commercially repurposed for use in the pipes and handles of the “iNSTIK ZUBAQ,” a cordless stick cleaner produced by Mitsubishi Electric Corporation. The move has put MHI in the lead in building a supply chain that includes reuse of difficult-to-recycle carbon fiber waste material in a mass-manufactured product. Effective use of resources has contributed to mitigation of environmental impact and protection of the global environment, thereby enhancing the Company’s corporate image.
Large frame gas turbine combustion technology enabling 20% hydrogen fuel blending operation
Mitsubishi Heavy Industries, Ltd., Energy Systems
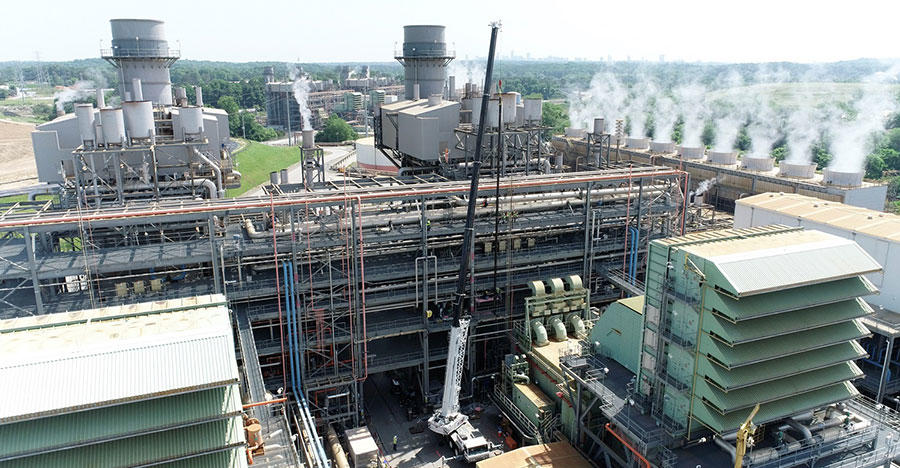
Plant McDonough-Atkinson in Georgia, USA
MHI has successfully demonstrated world’s largest hydrogen fuel blending operation in a high-efficiency large frame GTCC (gas turbine combined cycle) under both partial and full load conditions. The achievement was made based on the Company’s accumulated experience and technology developments in hydrogen combustion, and the technology was applied in M501G GTCC power generation plant in use in the United States. The demonstration proved a combustion stability with use of a 20% hydrogen fuel blend. With hydrogen-blended combustion using a dry low NOx combustor, a turbine inlet temperature equivalent to natural gas firing was maintained, and hydrogen firing successfully kept emissions within the compliant range. What’s more, while keeping emissions regulations, ability to lower the minimal operational load was also confirmed. This was the largest-scale test ever of hydrogen-blended fuel in a large frame GTCC, and it marked a major step toward achieving practical use of a hydrogen gas turbine.
For further information about the project, please visit: https://www.changeinpower.com/mcdonough/
Combustion system and control technology enabling high-efficiency incineration and volume reduction of diverse waste materials
Mitsubishi Heavy Industries Environmental & Chemical Engineering Co., Ltd., Engineering Division
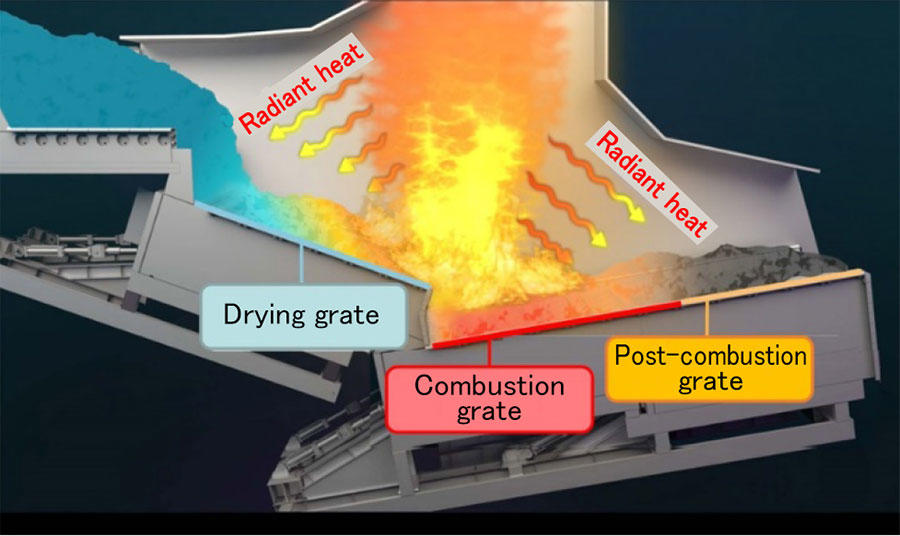
Stoker structure and incinerator
shape enabling continuous receipt of
radiant heat
MHIEC developed a V-shaped stoker type waste incinerator enabling low ignition loss (ratio of the unburnt content in the bottom ash), further optimizing the drying and combustion processes of the stoker type incinerators used in waste-to-energy plants. In order for the surface of the stoker grates to be directed at the center of the flame during all processes – drying, combustion and post-combustion – the incinerator is designed in “V-shaped” that leads to stable incineration as well as to reduce the volume of waste materials of diverse water content and other properties and states. The result is reduced ignition loss and increased incineration capacity per unit area of the stoker. In addition to greater combustion performance, the proprietary V-shaped structure simultaneously enables a more compact unit.
Structural optimization technology enabling quiet automotive double scroll turbochargers
Mitsubishi Heavy Industries, Ltd., Research & Innovation Center
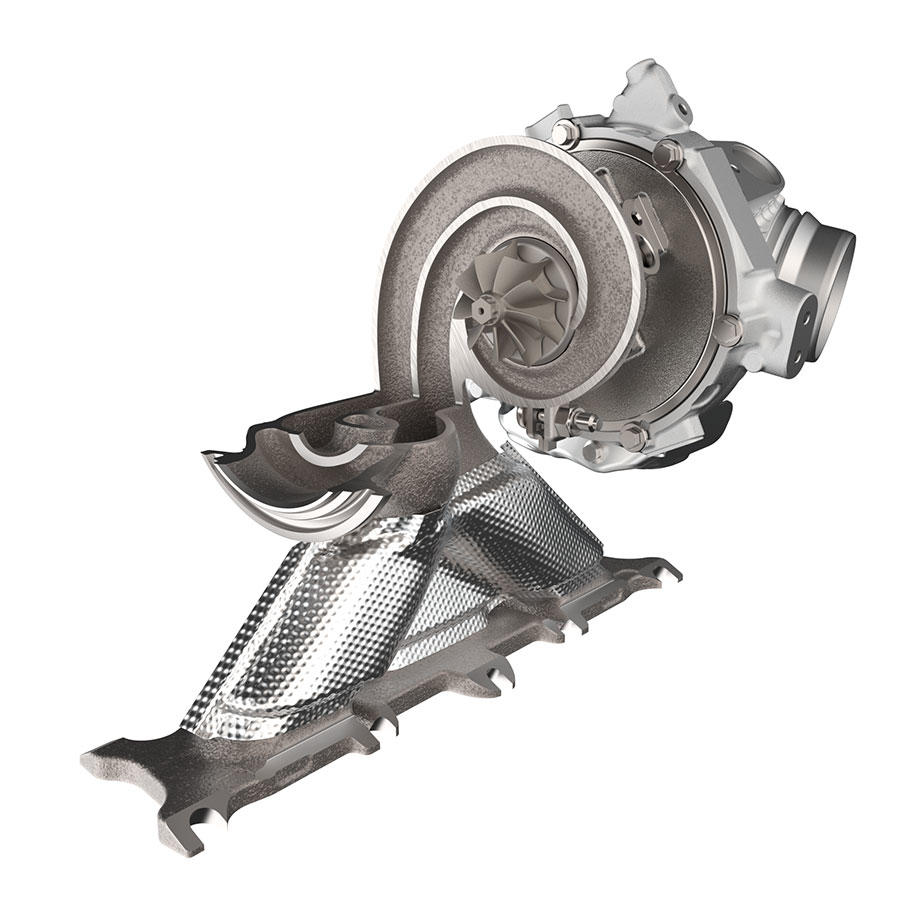
Automotive Double Scroll
Turbocharger
MHI has achieved low noise in automotive double scroll turbochargers by aerodynamic, vibration and other technologies. Noise is an issue of critical importance, and its resolution is expected to attract large-scale orders in the European market. Achieving low noise and low fuel consumption by high turbine performance was made possible by pursuing the optimized shape of the turbine blade’s leading edge and optimal number of blades to minimize noise when installed in the customer’s automotive engines. Noise reduction level was -13dB while maintaining aerodynamic performance. The low-noise concept is also applicable for reducing the aerodynamic noise of other turbomachines.
Advanced light water reactor “SRZ-1200,” contributing to realization of a carbon neutral society and enhancement of energy security
Mitsubishi Heavy Industries, Ltd., Nuclear Energy Systems
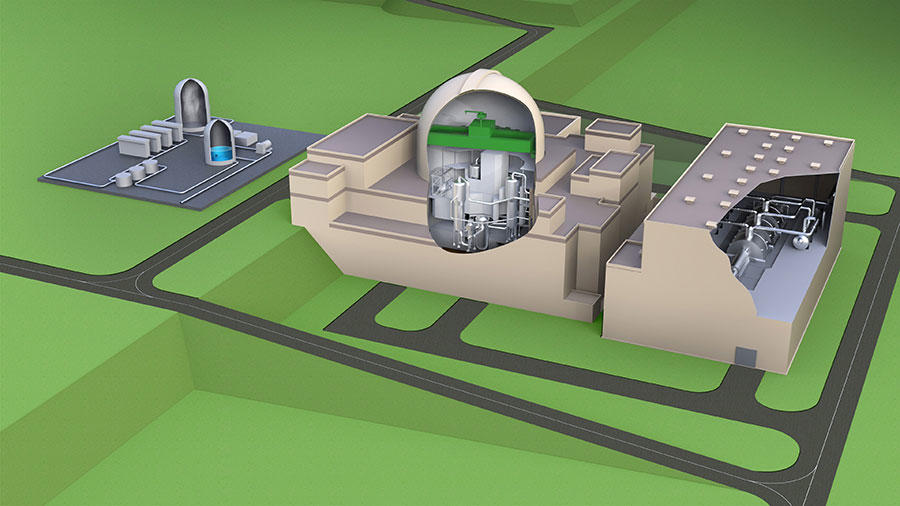
Advanced light water reactor
“SRZ-1200”
MHI, in collaboration with four Japanese utilities employing pressurized water reactors (PWRs)(Note), is developing the conceptual design of an advanced light water reactor, the “SRZ-1200.” The SRZ-1200 achieves the world’s highest level of safety through incorporation of new safety mechanisms, including a core catcher – the world’s newest technology for molten core materials of a nuclear reactor – and MHI’s proprietary system to prevent emissions of radioactive materials. These and other innovations came on the back of the Company’s accumulated technologies and expertise in the construction and maintenance of all 24 PWRs in Japan. Through proactive publicity – including press releases, promotional videos, etc. – MHI broadly conveys its specific initiatives and outstanding technological capabilities in the nuclear energy business, toward realizing a carbon neutral society and enhancing energy security, and these activities have contributed solidly to enhancement of MHI Group’s public image.
- Hokkaido Electric Power Co., Inc.; The Kansai Electric Power Co., Inc.; Shikoku Electric Power Co., Inc.; Kyushu Electric Power Co., Inc.
The “Best Innovation” program has been held annually since 2003 to recognize innovative new products, services, technologies, businesses and environmental activities within MHI Group, and going forward the Company will continue to pursue further technological innovations. By providing the world with outstanding products and technologies, MHI Group looks to simultaneously contribute to realization of a sustainable society and to enhance its corporate value through the long term.
About MHI Group
Mitsubishi Heavy Industries (MHI) Group is one of the world’s leading industrial groups, spanning energy, smart infrastructure, industrial machinery, aerospace and defense. MHI Group combines cutting-edge technology with deep experience to deliver innovative, integrated solutions that help to realize a carbon neutral world, improve the quality of life and ensure a safer world. For more information, please visit www.mhi.com or follow our insights and stories on spectra.mhi.com.