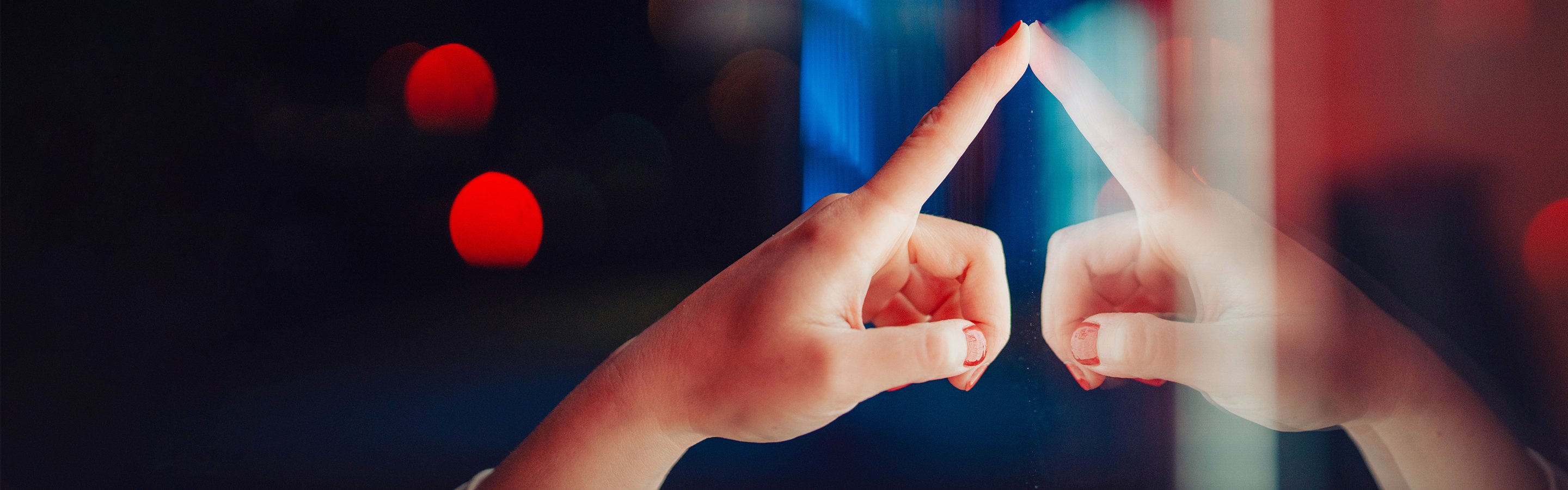
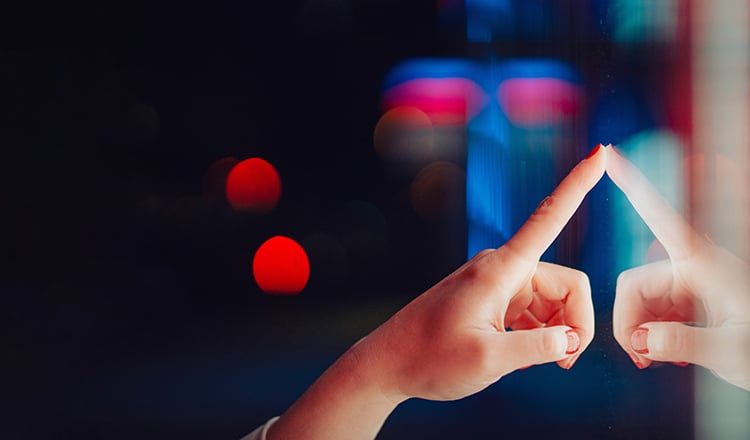
INSIGHTS
MHI’s unique perspective on the global trends impacting technology, industry, decarbonization, and more.
Carbon Neutral World
Carbon Neutral World
Carbon Neutral World
Security & Exploration
Carbon Neutral World