Closing in on the latest research on a tire inspection machine that underpins the growth of a motorized society.
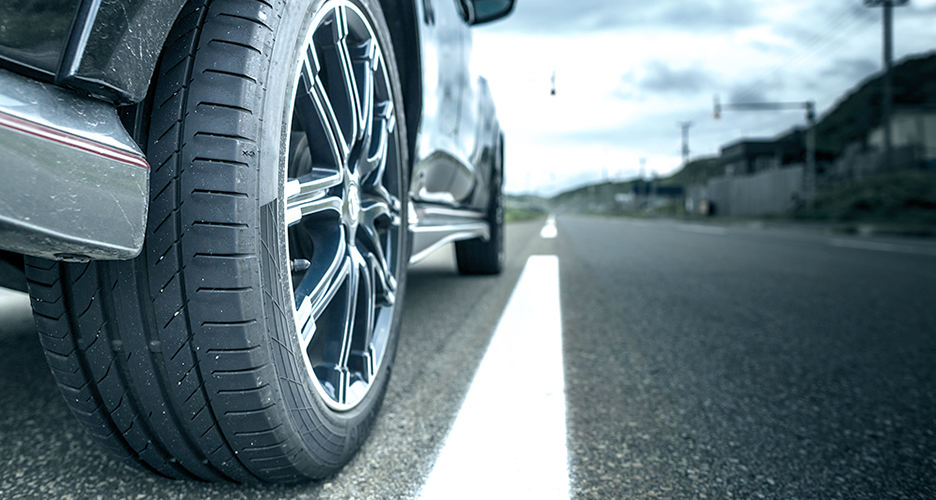
Story1
The tires driving the world’s roads have to be checked for proper balance.
Does the traveling performance of an automobile depend on its tires?
Safer, more fuel efficient, more pleasant to drive---. The car has evolved rapidly ever since its very first days. The tires controlling the travel of a car plays a vital role in the upgrading of the car’s performance. In addition to eco-tires with excellent fuel efficiency, recent years have seen the advent of many high-performance tires offering additional value with properties such as improved grip performance, comfort, and noiselessness. Year by year, tire manufacturers renew their determination to enhance performance and quality.
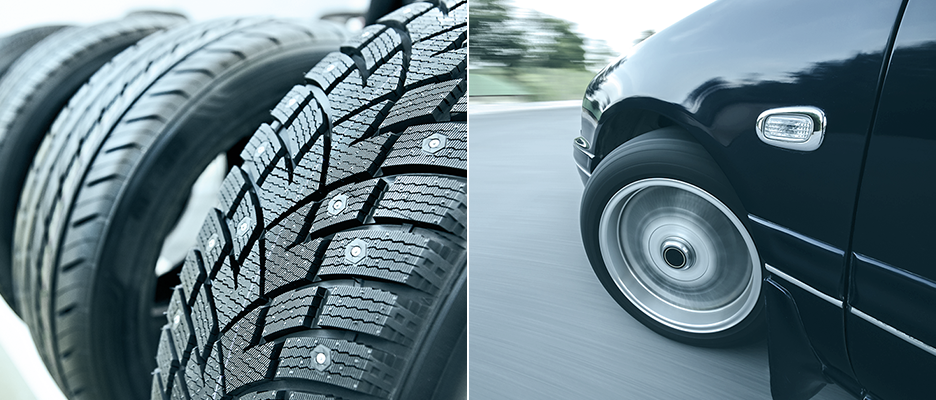
To support the production sites of tire manufacturers, Mitsubishi Heavy Industries Machinery Systems (MHI-MS) has been wholly manufacturing and selling production machinery used exclusively for tires at all stages of tire production from the mixing of the raw materials (rubber, carbon, etc.) to the final quality inspection.
Identifying marks on tires
A completed tire is marked with a yellow or red symbol. The mark is proof that the tire has cleared a rigorous quality inspection. A yellow mark is generally a location indicating the “light point,” the part of the tire where the tire weight is lightest.

In car production and maintenance shops, thorough steps are taken to match the yellow marks with the heaviest parts of the wheels when the tires are fixed. This matching keeps the weight of the tires in balance.
Partial weight deviations are impossible to avoid even in tires that appear to perfect circle. Various processes in production inevitably cause them.
The DBM (dynamic balance machine) for the testing of tires verifies the quality by measuring the weight balance of tires at the final stage of the manufacturing process. The machine plays an active role in production.
T.T, is in charge of design, offers the following explanation.
“A tire with weight unbalance will generate unwanted vibration as the car travels. The vibration leads to troubles with ride comfort, such as a poor tire grip, steering wheel shake, and strong jolting of the car body. It can also seriously compromise safety. These problems underscore the importance of the DBM for confirming the final quality.”
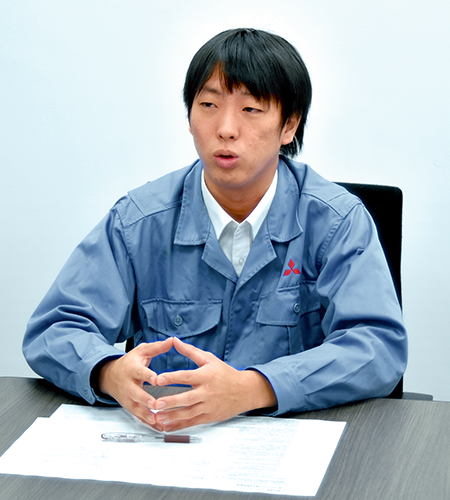
Production Equipment Designing Section
Machinery Engineering Department
Infrastructure Facilities Business Division
Story2
The DBM serves at the highest level of the tire manufacturing industry. But the accuracy and productivity of the machine still has plenty of room to get better.
A high-accuracy DBM with a novel mechanism has been developed.
The DBM prevents the market outflow of defective tires, supports tire productivity improvements, and ensures optimal tire mounting onto cars. The DBM has provided all of these benefits since the very first unit became operational back in around 1990.
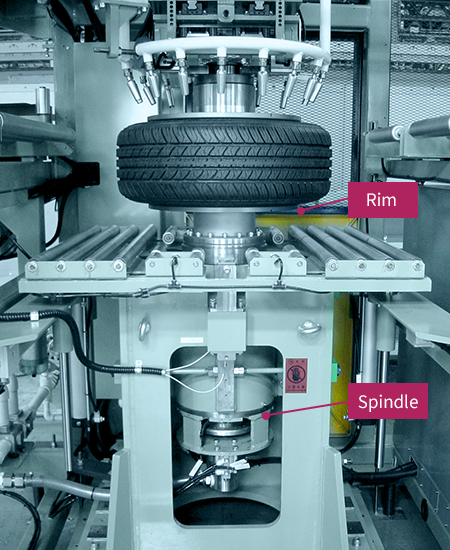
The DBM produced by MHI-MS has steadily evolved by offering improved measurement accuracy and faster adjustment to accommodate tires of different sizes during production.
A unique built-in motor method to contain the motor in the spindle was developed to suppress vibration and noise during operation of the DBM.
The industry’s highest measuring accuracy has been realized by stabilizing the machine. A weight difference of 1 gram or less can now be achieved in periods as short as 17 seconds per tire.
Mechanism of the DBM
The tire is mounted on the rim (part of wheel) of the spindle and rotated at a speed comparable to that of rapid road driving. Sensors perform the measurement by three-dimensionally detecting the value and degree of the unbalance parts.
The measurement keystone is the vibration of the DBM body itself.
Before the DBM is started, the vibration generated by the machine itself is measured with a weight and the measurement results are to be used as calibration parameter. A correct weight balance can be calculated by deducting these values from the values measured during operation.
The DBM, however, is always exposed to vibration. With time, natural frequency of the machine will vary gradually due to aging phenomena such as abrasion, etc. and changes in temperature and other environmental conditions in the production shop.
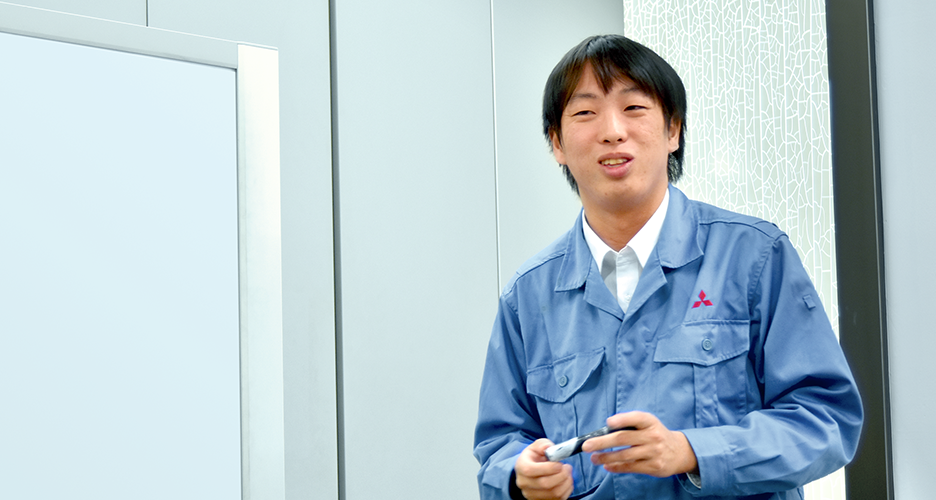
“If errors are generated in the initial calibration parameter and the actual parameter, the measurement error will be too great to permit the output of usable results. To ensure correct parameter appropriate to the actual conditions, calibration works to periodically correct the calibration parameter are required.”
The challenge to accelerate volume production
The enhanced automation of present-day tire production lines often enables operation around the clock. Many manufacturers, meanwhile, are carrying out “total inspections” that push the number of tires inspected by a single DBM up to about 3,000 per day, and in some cases 100,000 per month.
“Calibration works require abundant manpower and often hinder production efficiency by requiring production line suspensions in the shops. Starting from October 2015. MHI-MS began experimental research focused on multi-directional product improvements to prolong the periods the measurement accuracy could be maintained.”
Tire Manufacturing Process (an Example)
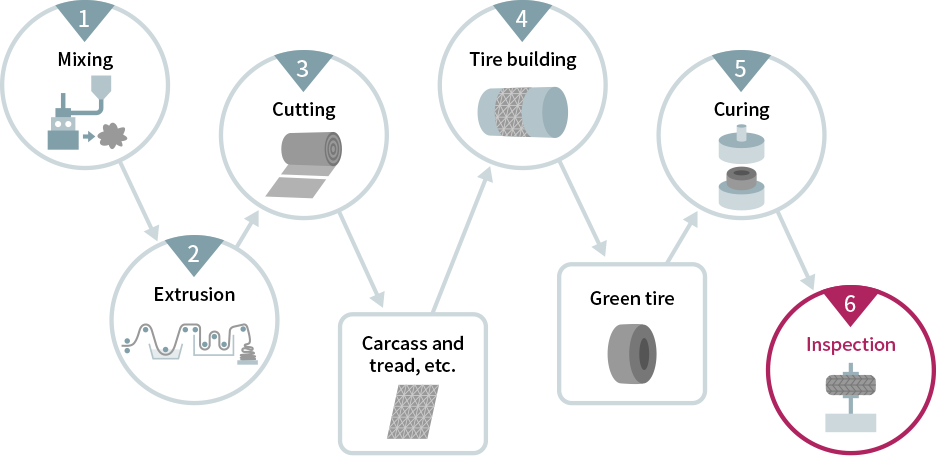
MHI-MS designs and produces a wide variety of tire manufacturing machines, from those for Mixing the raw materials, to those for curing and inspection. Production volumes of up to several thousands of tires a day are supported.
Story3
What are the “rules” required for self-diagnosis and automatic correction?
The first approach taken was mechanical viewpoint.
This research started from work to closely investigate the fundamental factors that lead to deviations in measurement accuracy. Every cause was determined and characterized one by one. They are; changes of temperature and humidity in the production shop, variations in the condition of the machinery, the adhesion of fractional dust and oil, etc. all had effects.
The first step to resolve the causes identified was to improve the tire spindle, a strong source of vibration and noise.
“Now that the DBM has gone through years design upgrades, the quality and accuracy levels of the parts are closer than ever to perfect. Even if we achieve further improvements through minor adjustments, I think it will be difficult to come up with new fundamental solutions from the viewpoint of cost-benefit performance.”
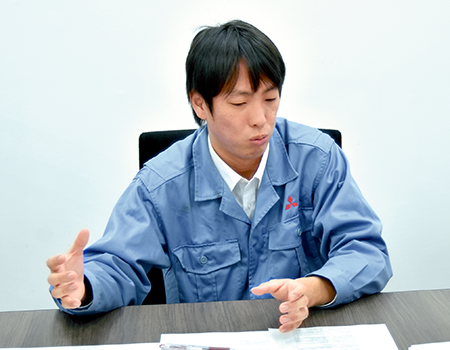
Problem-solving from the digital viewpoint.
In his search for a breakthrough, he chanced upon the idea of renovating the software rather than the hardware. A newer method of software calibration had the potential to replace a process that previously relied human-power. If the DBM could self-diagnose changes in its own conditions and automatically correct the basic parameter, two challenging problems could be solved at one time: how can the calibration period be shortened and how can the accuracy be maintained for longer?
A self-diagnosing DBM, however, would have to operate in accordance with a set of “digital rules.” He studied the many types of data required to correctly measure variations in the state of the spindle. He chose one type to focus on intensively.
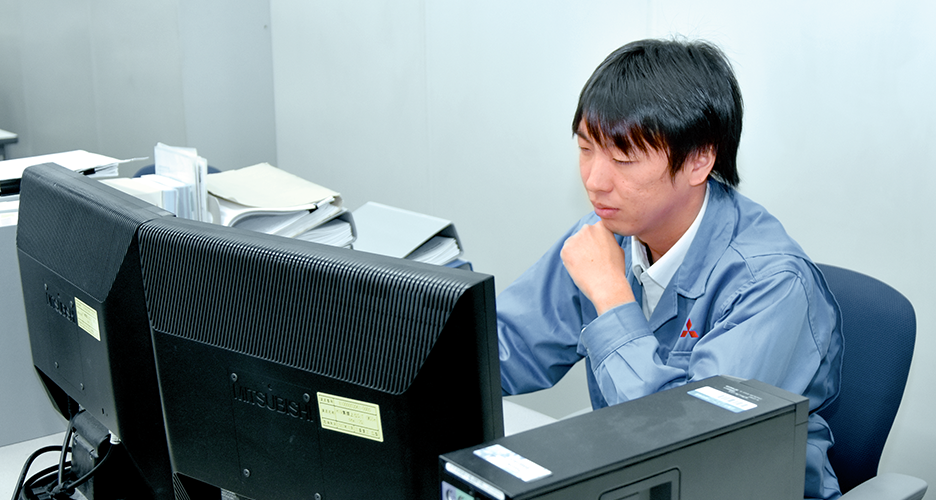
“If the spindle is continuously used, a part of the unbalance and weight difference will stem from factors that cause the same problems in tires. By incorporating an error level of 1 gram of deviation or less as a monitoring parameter, I believed that the DBM could self-diagnose differences from the basic parameter and then make automatic corrections.”
Story4
A fresh new idea became the hint for innovation.
At one point T.T applied knowledge he learned as a student to his work at the development site.
He says that this epoch-making approach yields successful results little by little. Even at this early stage, he expects one day to apply the approach in an actual product.
He recounts his experience in grad school specializing in precision engineering and developing a device with driving at nanometer order precision:
“I learned to grasp things not only through the details of their mechanical structures and operational precision, but also from digital perspectives by changing the observation points. While I still have a long way to go in my current experiments and research, I can use the knowledge I acquired as a student to get there. That pleases me and fills me with confidence.”
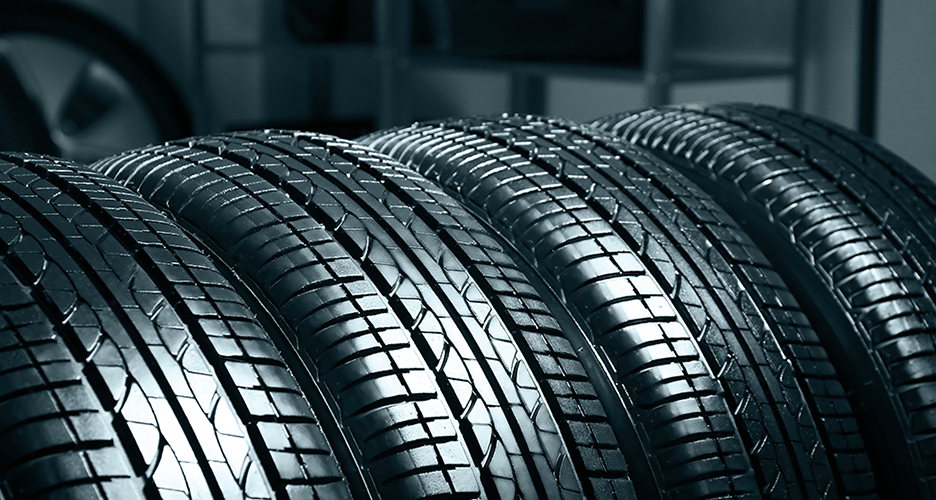
Fresh ideas and technologies from outside the field sometimes go into the development of an epoch-making product.
In many case in the past, young engineers like him or external manufacturers collaborating with MHI-MS in technical collaborations have come up with fresh ideas that have led to breakthroughs in problem-solving and the inception of new products and capabilities.
Story5
The next move is to innovate the basic structure at the core.
The tires of the future will determine the performance of cars.
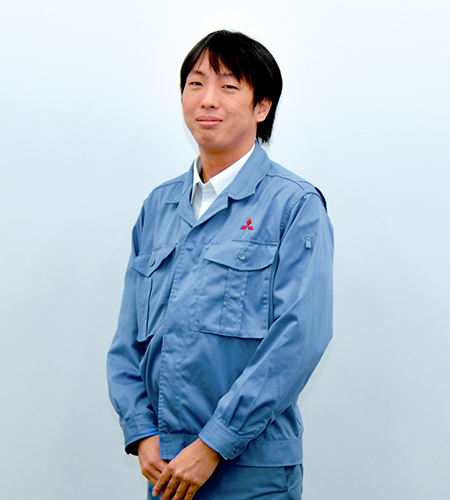
The current research has led to a reduction of working time by approximately 15% compared with a conventional DBM through simplification of the earlier calibration process that relied on human-power. Tire productivity has been much enhanced.
More fundamental product improvements are being studied, including the introduction of a new technology and a renewal of the DBM configuration.
“The final target is to support volume production of high-quality tires by eliminating the calibration work. A university laboratory in a different field may very well come up with the next-generation technologies necessary for such a technical innovation. A collection of knowledge outside of the mechanical field and channels for information exchange with surrounding fields will always be key.”
The car business is going through a dramatic centenary change with the rise of automated driving and electric vehicles.
The next-generation tire will continue to evolve, along with the key technologies to inspect it.
The DBM of MHI-MS will be further developed to support tomorrow’s car society.
PRODUCTS COVERED
Development Story
Next-Generation Multistory Parking Lot installed underground in the inner-city - Birth of the Mitsubishi Cell Park (Two-Lift Type) -
From the site of MC development, a new corrugated board box making machine that is responsible for the production of corrugated boxes that supports our lives and economy
R&D
- Research System and Development Base
-
Strategic Innovation
- The world’s first! A Next-Generation ERP to Realize the Roads of Tomorrow in Singapore
- Meeting the needs of global logistics! The EVOL box making machine enables the high-speed mass production of corrugated board boxes.
- Keep a drink delicious and fresh! A carbon coating that evolves PET bottled beverages.
-
From the research and development sites
-
Development Story
- Next-Generation Multistory Parking Lot installed underground in the inner-city - Birth of the Mitsubishi Cell Park (Two-Lift Type) -
- From the site of MC development, a new corrugated board box making machine that is responsible for the production of corrugated boxes that supports our lives and economy
- Closing in on the latest research on a tire inspection machine that underpins the growth of a motorized society.
-
Innovators
- A magnitude 7 earthquake is faithfully reproduced in every detail! “Advanced hydraulic and control technologies” to shake full-scale medium-rise buildings.
- Rapid, beautiful, economical! A newspaper offset press developed to lead the world.
- Generate novel experiences in large-scale facilities that inspire and amaze people and awaken them to new possibilities. Frontline “Moving Technology.”
-
Development Story
- Mitsubishi Heavy Industries Technical Review