クルマ社会の発展を足元から支える「タイヤ試験機」の最新研究に迫る
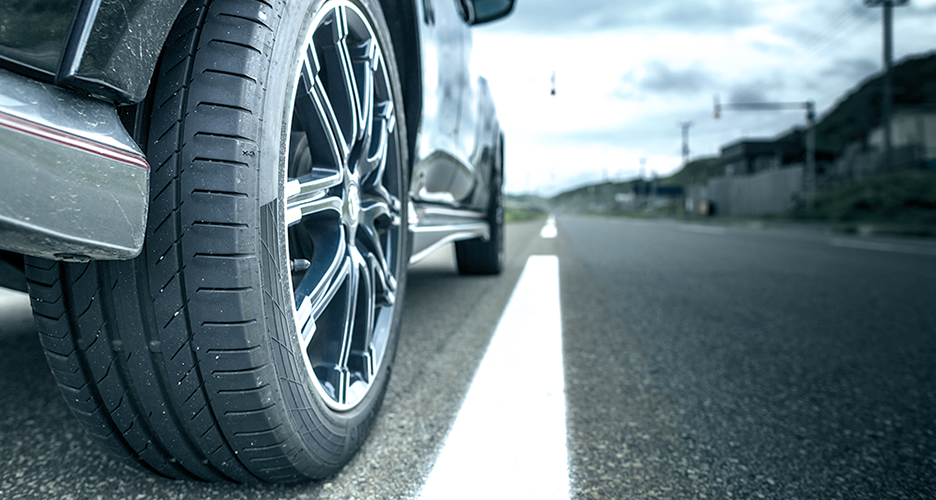
Story1
世の中のタイヤは、必ずバランスがチェックされている
走行性能はタイヤで変わる?
より安全に、もっと低燃費に、ドライブをさらに楽しく――。自動車は誕生以来、日進月歩の進化を続けてきた。そしてその性能向上に欠かせないのが、車の走りをつかさどる「タイヤ」だ。
特に近年燃費に長けたエコタイヤをはじめ、グリップ性能・快適性・静粛性など高性能・高付加価値なタイヤも数多く登場し、タイヤメーカーの性能と品質へのこだわりは高まり続けている。
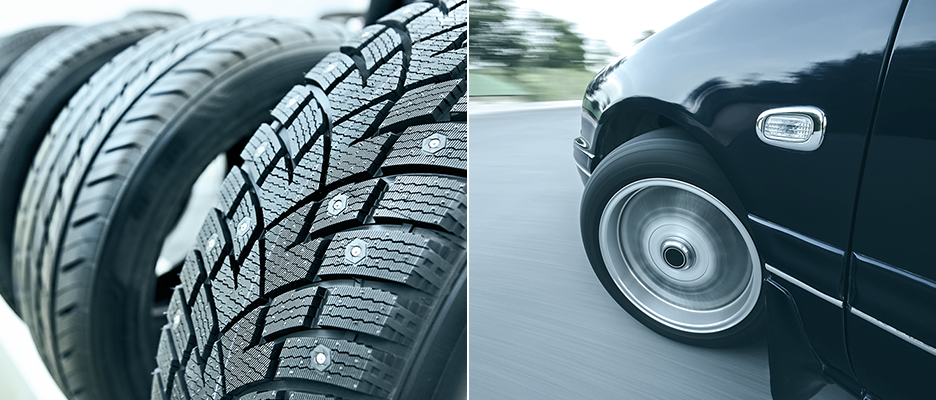
三菱重工機械システム(MHI-MS)は、そんなタイヤメーカーの生産現場をサポートするべく、タイヤの原料(ゴムやカーボンなど)を混ぜ合わせる混練から最終的な品質検査まで、タイヤ専用の生産機械をトータルに製造・販売してきた。
タイヤについたマークの正体
完成したタイヤには黄色や赤のマークがついている。実はこのマークこそが、厳しい品質検査をクリアした証。たとえば、一般的に黄色は、軽点と呼ばれる「タイヤの重量が一番軽くなっている部分」を指す目印だ。
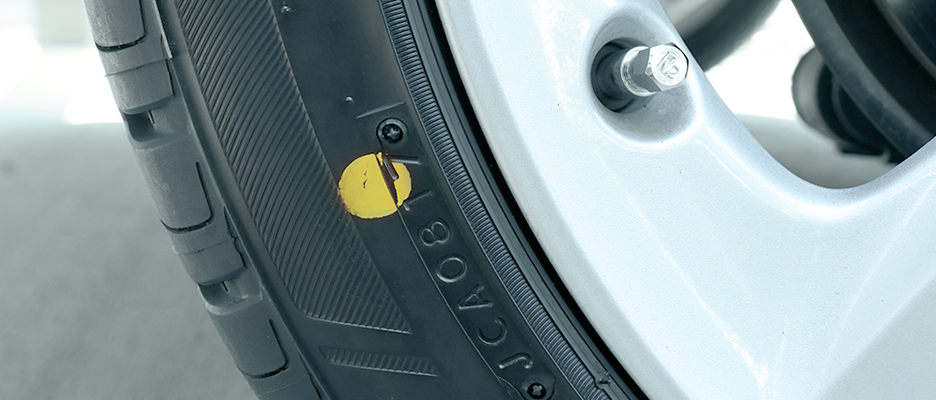
車の生産・整備工場ではタイヤの重量バランスを保つために、タイヤ装着の際に黄色いマークとホイールの最も重い部分を合わせる作業が徹底されている。
一見きれいな円形のタイヤも、さまざまな生産工程を経るなかで、どうしても部分的に重さの偏りが生じてしまう。
そこで活躍するのが製造工程の最終段階で、タイヤの重量バランスを計測して品質確認を行う、タイヤ試験機「DBM(ダイナミックバランシングマシン)」だ。
設計を手がけるT.Tは、こう語る。
「重量バランスが悪いと走行時に不要な振動が発生します。そうすると、タイヤのグリップが効き難く、ハンドルがブレたり、車体のゆれが強くなったりと乗り心地だけでなく、安全上大きな問題が発生してしまいます。
だからこそDBMによる最終品質確認が重要なのです。」
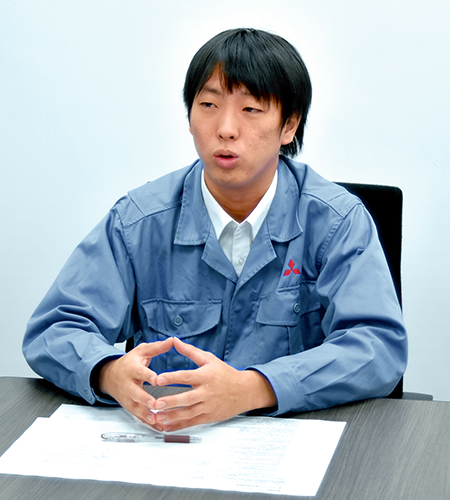
機械技術部 生産機械設計課
T.T
Story2
業界最高水準を誇るDBM
その精度と生産性はまだまだ伸ばせる
独自機構の採用で、高精度なDBMを開発
タイヤの生産性向上と車への最適な装着をサポートすると共に、不良タイヤの市場流出を防ぐ。
DBMがそうした役割を担って世の中に誕生したのは、1990年頃のこと。
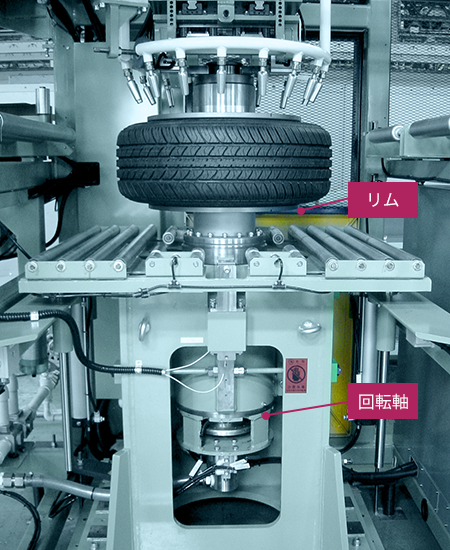
MHI-MSのDBMは計測精度とスピードの向上、そしてあらゆるタイヤサイズへの対応をテーマに掲げて進化を遂げた。
たとえば、DBMが稼働する際の振動ノイズを抑えるために、回転軸にモータを内蔵した独自のビルトインモータ方式を開発。
機械を安定させることで業界最高水準の計測精度を実現すると共に、タイヤ1本あたり最短17秒で、1グラム以下の重量差まで弾き出すことに成功したのだ。
DBMのメカニズム
タイヤを回転軸のリム(ホイール部分)にセットし、走行時のように高速回転させて、どこがアンバランスで、どの程度重さのムラがあるのかをセンサーで3次元的に検知して計測する。
“計測の要”はDBM自体の揺れ
DBMは稼働させる前に、おもりで機械自体が発する振動を測り、基礎データとして設定する。これを稼働時の計測データから差し引くことで、正しい重量バランスを算出する。
しかしDBMは常に振動にさらされているため、摩耗などの経年変化や生産工場の温度変化などの環境変化が原因で、徐々に機械固有の振動数が変化してしまう。
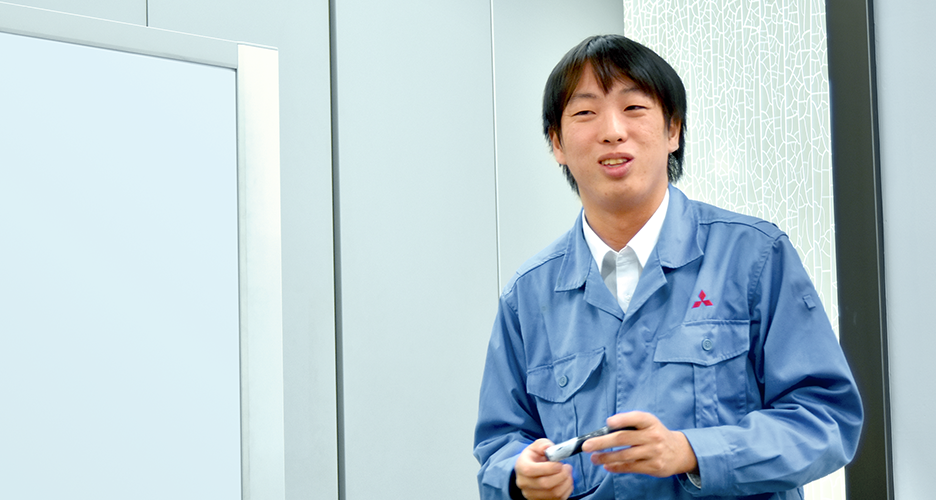
「最初の基礎データと実際の振動に誤差が生じると、正確な計測ができず役に立ちません。
そこで実情に合わせるために、定期的に基礎データを修正する「校正作業」が必要なのです。」
大量生産を加速するチャレンジ
現在タイヤの生産ラインはオートメーション化が進み、24時間体制で稼働するケースも珍しくない。さらにメーカーの多くが「全数検査」を行うため、1台のDBMが検査するタイヤは1日約3000本、1カ月に10万本に及ぶことも。
「校正作業は人手がかかるうえに、工場のラインを止めてしまうので、生産効率に与える影響が大きい。そこで計測精度の維持期間を長くするために、2015年10月から多角的な製品改良を目指す試験研究がスタートしました。」
タイヤ製造工程(1例)
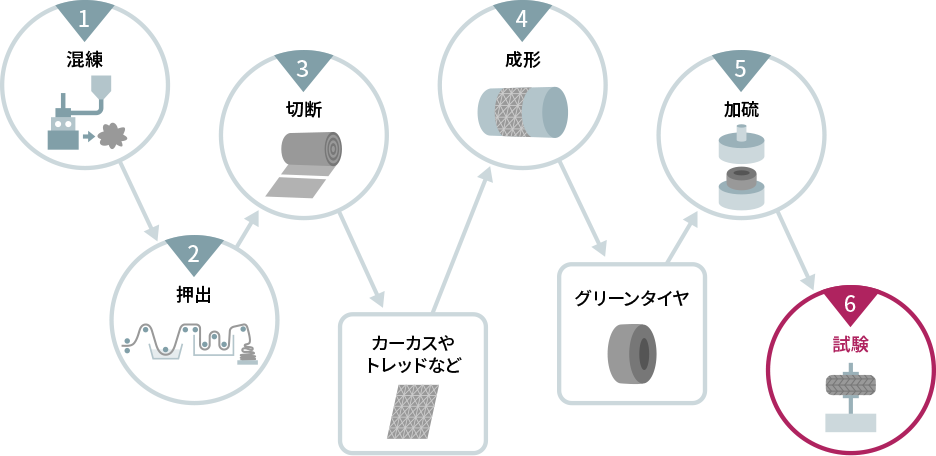
MHI-MSではタイヤ原料の混練から、加硫、検査まで多種多様なタイヤ製造機器を設計・製造。1日数千本に及ぶ大量生産をサポートしている。
Story3
自己診断&自動補正に必要な“ものさし”とは?
まず取り組んだのは、機械的なアプローチ
この研究は計測精度の「ズレを引き起こす根本的要因」を洗い出すことから始まった。
生産工場の温度・湿度、機械の状態変化、わずかなゴミや油の付着など、一つひとつを検証。
こうして判明した要因を解消すべく、まずは振動ノイズを生みやすい「タイヤ回転軸の改良」に着手した。
「しかし長年アップデートを重ねたDBMは、部品の完成度が極めて高い。そのためマイナーチェンジである程度改善はできても、根本的な解決は費用対効果の面で難しいと判断しました。」
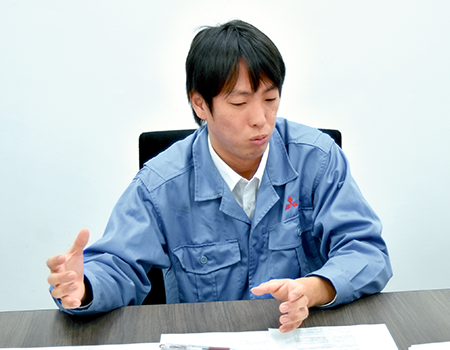
デジタルな切り口で課題解決を目指す
打開策を模索する中、ハード面よりソフト面、つまり人力に頼っていた校正方法を刷新できないかと考えた。
DBMが自ら状態の変化を診断し基礎データを自動補正することが出来れば、“校正時間の短縮”と“精度維持期間の延長”という、2つの課題を一気にクリアできる。
しかしそれには“デジタルなものさし”が必要だ。回転軸の状態変化を正しく測るために必要なデータをいくつも検討し、その中のひとつに着目する。
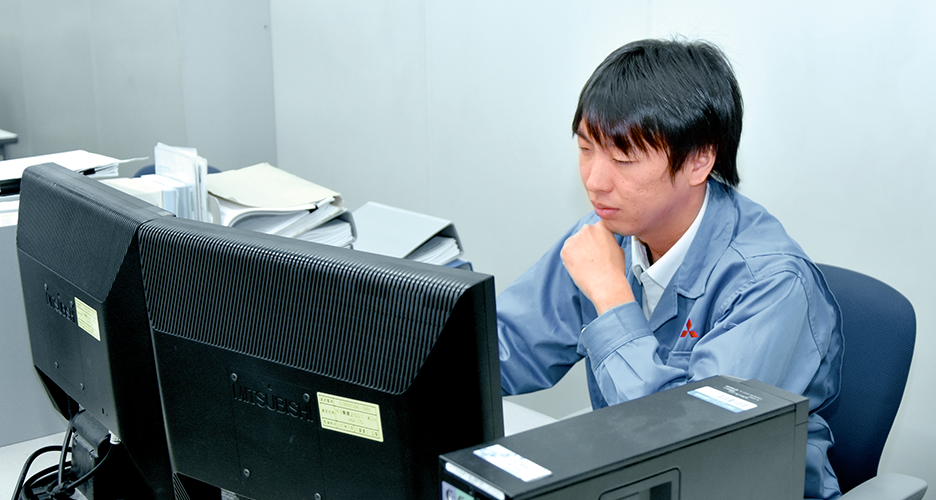
「タイヤと同様に、回転軸も使い続けるとアンバランスな部分や重量の違いが生じます。
1グラム以下の“誤差レベル”の偏りですが、これを「状態監視パラメータ」として取り込めれば、DBMが基礎データとの差を診断して、自動補正できると考えました。」
Story4
新鮮な発想の導入が、イノベーションのヒントに
学生時代の知見が、開発現場で活きる瞬間も
この画期的な取り組みは少しずつ成果を上げており、製品導入レベルを目指していま現在も進行中だという。
大学院時代に精密工学を専攻し、ナノレベルの動作精度が求められる装置の開発を行っていたT.Tはいう。
「そこで得たのは機械構造や精度だけでなく、視点を変えてデジタルな側面でも物事をとらえるという発想でした。今回の試験研究はまだまだ道半ばですが、学生時代に培った知見を仕事に活かせることに喜びを感じ、また自信にもなりました。」
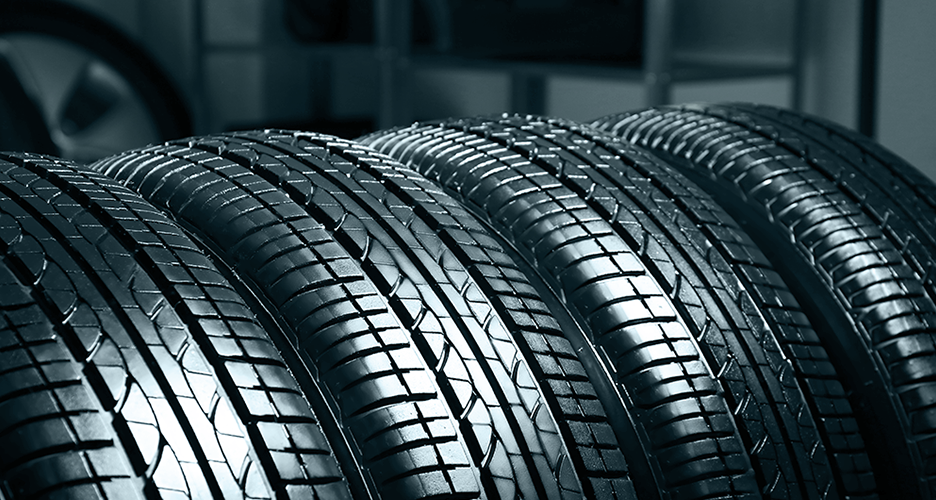
画期的な製品開発には、社外の斬新なアイデアや技術を活用するケースも珍しくない。
事実、T.Tをはじめとする若手技術者のひらめきや外部メーカーとの技術連携が、課題解決の突破口となり、新製品や新機能の誕生につながった事例も数多くあるのだ。
Story5
次の一手は「核」となる基本構造の革新
車の性能を決めるタイヤの未来
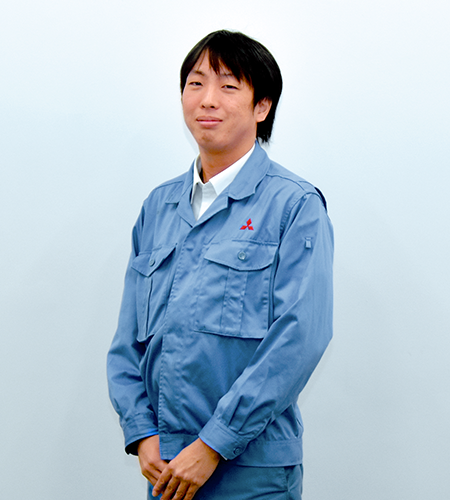
現在の研究成果は人力に頼っていた校正工程の簡略化で、作業時間が従来比で約15パーセントの削減につながり、タイヤの生産性向上に大きく貢献している。
今後はそれだけでなく、新技術の導入やDBMの構造リニューアルといった、より抜本的な製品改良を検討中だ。
「最終目標は校正作業を無くして、高品質なタイヤの大量生産をサポートすること。
そうした技術革新に必要な次世代テクノロジーは、異分野の大学の研究室が先行している可能性も十分あります。
ですから、機械分野にはない知見の収集や、周囲との情報交換は常に欠かせません。」
自動運転や電気自動車の台頭で、100年に1度の変革期を迎えている自動車業界。
これに伴い次世代のタイヤはますます進化し、その品質検査も必要不可欠となる。
車社会の未来を支えるために、MHI-MSのDBMはさらなる進化を目指す。