Pressurized Water Reactor (PWR):Improvement and Development
Improvement and Development
Enforced Operability
Highly reliable Instrumentation and control(I&C) systems with extended capabilities and operability are indispensable for the safe and stable operation of a nuclear power plant. The operability of Mitsubishi PWR plants has been improved through utilization of the latest computer and electronics technologies and development of easily maneuverable main control boards and digitalized reactor control/protection systems. For existing plants, MHI has performed complete replacement of the main control boards to enhance operability, as well as a renewal of the instrumentation/control systems and cables in plant.
Advanced Instrumentation and Control System
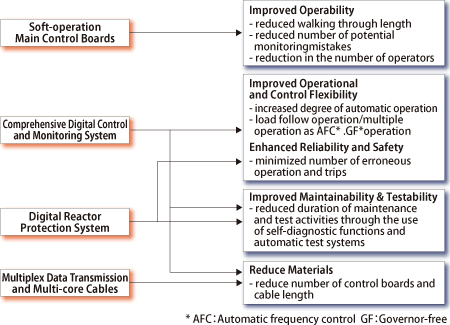
Soft-operation Main Control Boards
- Improved Operability
- reduced walking through length
- reduced number of potential monitoring mistakes
- reduction in the number of operators
Comprehensive Digital Control and Monitoring System
- Improved Operability and Control Flexibility
- increased degree of automatic operation
- load follow operation
- operational multiplicity, such as AFC/GF*operation
- Enhanced Reliability and Safety
- minimized number of erroneous operation and trips
- Improved Maintainability & Testability
- reduced duration of maintenance and test activities through the use of self-diagnostic functions and automatic test systems
- Reduce Materials
- reduce number of control boards and cable
Digital Reactor Protection System
- Improver Operability and Control Flexibility
- increased degree of automatic operation
- daily load follow operation
- operational multiplicity, such as AFC/GF*operation
- Enhanced Reliability and Safety
- minimized number of erroneous operation and trips
- Improved Maintainability & Testability
- reduced duration of maintenance and test activities through the use of self-diagnostic functions and automatic test systems
- Reduce Materials
- reduce number of control boards and cables
Multiplex Data Transmission and Multi-core Cables
- Reduce Materials
- reduce number of control boards and cables
- AFC:Automatic frequency control, GF:Governor-free
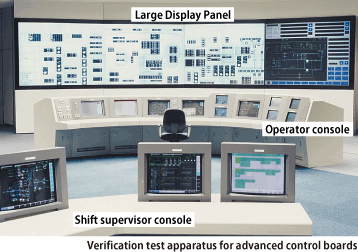
Maintenance Technology
Mitsubishi keeps a close eye on every facility, component, device, and subcomponent after delivery of the plant, for the benefit of customers, based on extensive experience and sound technology. Mitsubishi continues to enhance the safety, reliability, and economy of nuclear plants by introducing improvements at every level.
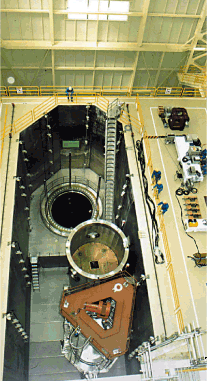
Examination/Inspection Technology
Mitsubishi continues to develop and improve diagnostic and inspection technologies and equipment, based on the extensive experiences accumulated in more than 30 years by inspecting the major facilities within nuclear power plants. Mitsubishi is developing several advanced inspection technologies such as; the development and application of remote-operable, intelligent robot systems to reduce radiation exposure of workers; the development of high-speed inspection systems to shorten periodical inspections; the application of high-speed data processing systems employing the latest computer technology; and the development of high-precision inspection equipment for improved component integrity evaluation.
Intelligent ECT System
Steam Generator Tube Inspection System
Fully automatic,high-speed inspection system with intelligent ETC prove.
The intelligent ECT system is used for the inspection of heat transfer tubes of the steam generator, major equipment of the PWR plant. Higher precision inspection capability is realized with the same inspection speed(400 mm/s) as conventional high-speed inspection system. The advanced analysis system is also developed that can conduct 100 percent total height inspection for heat transfer tubes, which enabled fast and precise analysis of large volume inspection data. Currently, the majority of domestic PWR plants adopt this inspection system. Furthermore, PWR plants in the US and Taiwan have began to adopt the system.
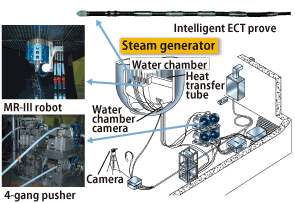
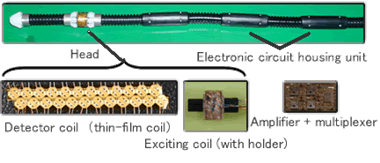
- Technology on Degradation,Repair,and Replacement
- Mitsubishi is developing and deploying technologies to repair or replace components that have or anticipated to have degraded by aging, or to mitigate degradation by minimizing the wear.MHI backs the development of these technologies with its comprehensive technical capabilities in the design of remote operation equipment and electro-mechanics, as well as its expertise in basic technologies such as welding and machining.
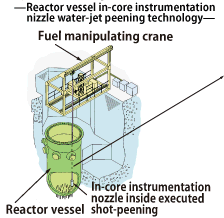
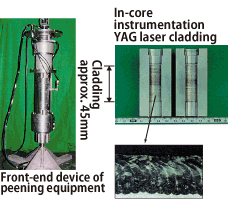
Technology on Degradation,Repair,and Replacement
World's first All-in-one-piece replacement work of PWR reactor internals was completed. A new extraction method was adopted that can remove the reactor internals without splitting and cutting.
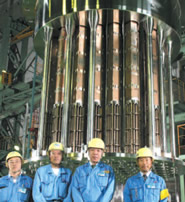
MHI completed world's first all-in-one-piece replacement work of the upper and lower reactor internals in Ikata Unit 1(566 MW) of Shikoku Electric Power Company. The replacement with reactor internals of the latest design was executed to accommodate the increased number of control rods needed for adopting high burn-up fuel, and to perform preventive maintenance in order to prevent damage of baffle former bolts fitting the baffle plate in the reactor internals. Damaging incident of the kind caused by stress corrosion cracking(SCC) was reported overseas. The development of a new replacement process that extract the existing reactor internals from the reactor vessel without splitting and cutting in the air enabled the replacement to be achieved with shorter period(five months) and with significantly reduced radiation exposure of workers.